KLINGER Dichtungstechnik 新型精加工系统
KLINGER克林格集团密封材料工厂 KLINGER Dichtungstechnik 开发了一套全自动化精加工系统,用于密封板材的生产。该系统由公司自主设计建造,实现了从板材上料、修边、定长切割、印刷到码垛的全流程自动化,并集成了 AI 质量控制,大幅提升了生产效率与可持续性。
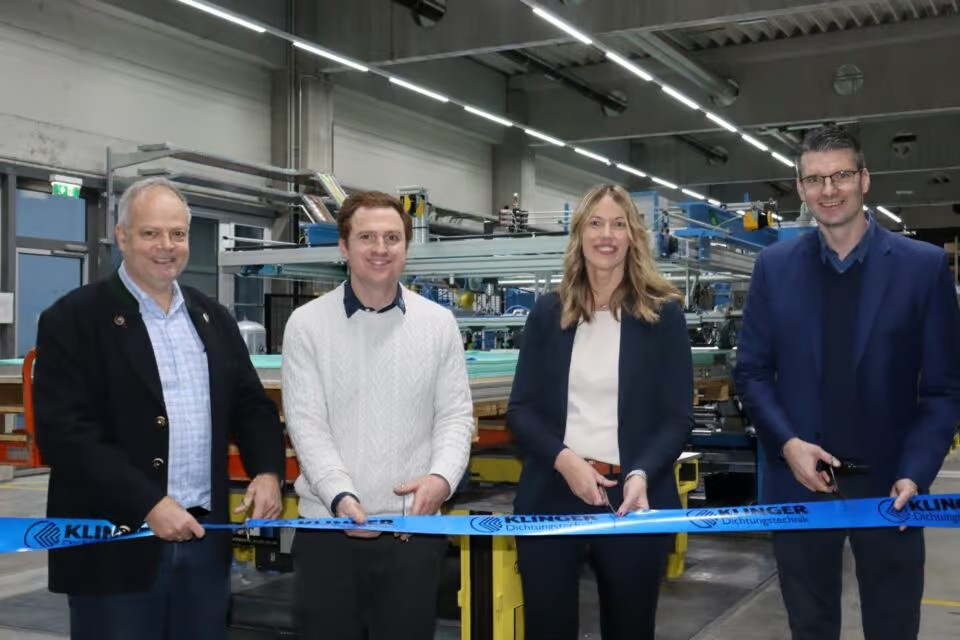
背景及工作原理
新设备负责将密封板材材料从压延机输送到托盘的整个流程,包括修边、将板材切割成客户指定的长度、印刷产品标识、质量控制(包括自动剔除检测)以及码垛。目前由于包装需要依照客户需求进行定制还需手工完成,其余流程均采用自动化。新设备使得整个生产流程大幅提速,循环时间从 40 秒缩短至 25 秒,生产速率从每小时 80 张提高到 130 张。
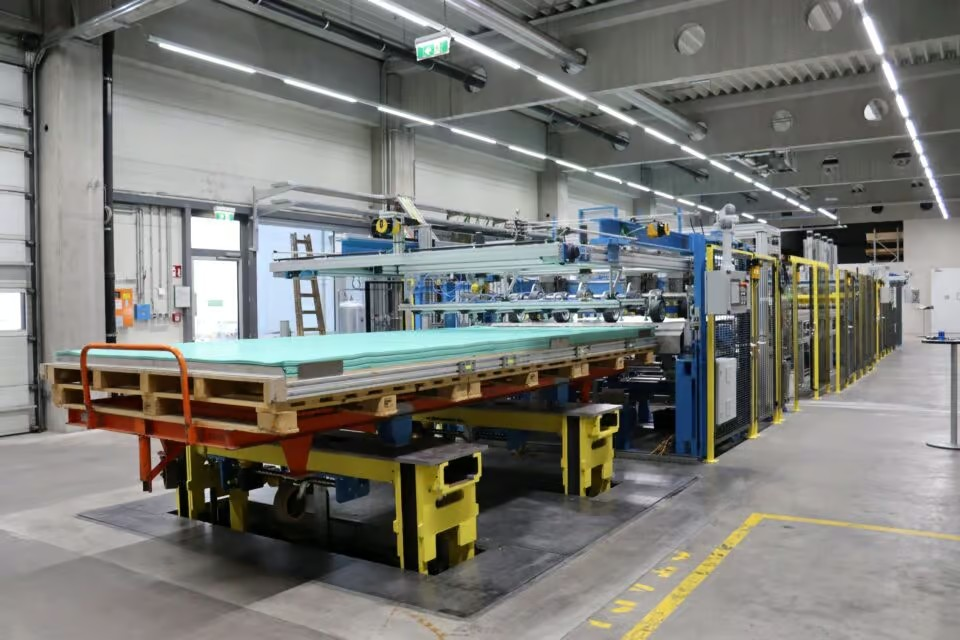
系统核心功能与技术流程
全流程自动化处理
- 板材定位:系统能够识别料架,通过四个螺旋千斤顶将其提升,并精准对齐顶部的密封板材。
- 气垫式送料:利用吸气抓手提起板材的同时,在板材底部吹气形成气垫,使材料能够轻松滑入进料辊。
- 修边:侧边的圆刀会切除板材的突出边缘,产生的废料会被粉碎并重新投入生产流程,以最大限度减少浪费。
- AI 视觉检测:板材通过搭载 8K 分辨率线扫描相机(每侧 3 台)的 AI 视觉系统,该系统基于 YOLOv11 卷积神经网络,能以低于 0.1 毫米 / 像素的分辨率实时检测缺陷,如褶皱等,并实时判断板材是否合格。
- 印刷:采用柔版印刷工艺,通过一个 15 公斤的滚筒在密封板材的底面印制产品标识。
- 定长切割:冲击剪切机会根据订单指定的尺寸,将板材切割至最终规格。
- 码垛:机械臂会将合格的板材堆叠在托盘上,而不合格的板材则会被放置在单独的堆垛中。
关键技术及参数
加工尺寸:最大可处理 2 米宽、4.5 米长的板材,同时也兼容英制规格。
输送速度:最高可达 60 米 / 分钟,系统配备了 39 台伺服电机,总功率约为 100kW。
自动化集成:整个系统的搭建涉及铺设 2.5 公里的电缆,设计 520 份技术图纸和 350 页的电路图,由约 25,000 个独立零件组成。
AI 视觉系统:质量控制的核心
该系统的突破性创新在于 AI 支持的视觉检测方案,由 KLINGER 内部团队开发,基于开源框架 YOLOv11。采用深度学习算法持续优化检测精度,可在 60 米 / 分钟的速度下实现 2000 毫米宽度的高分辨率扫描(每侧约 45 万条图像线)。通过神经网络 “抵消” 板材表面细微纹理,无需复杂照明系统,将照明成本从 2.2 万欧元降至 1000 欧元。实时识别褶皱、划痕等常见缺陷,自动剔除不合格品,确保 100% 质量追溯。
可持续性与成本效益
资源利用:废料回收再利用,减少原材料浪费;全电动伺服系统降低能耗。
人力优化:原工艺需多人操作,现仅需 1 人监控,大幅降低人力成本。
自研发驱动:因外部供应商成本上涨与创新限制,KLINGER 选择自主设计核心组件(如 PLC 程序由内部程序员编写),采用西门子伺服元件与皮尔兹安全系统,在保证性能的同时实现长期成本优化。